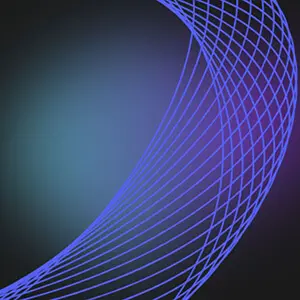
Total Materia provides access to over 570,000 materials and 25 million property records, powering the world’s most comprehensive solutions for materials selection, materials information management, ML-driven property prediction, compliance, and sustainability.
Overcoming challenges in finding reliable material data and precise material selection in engineering.
Facing the enterprise challenge of unifying diverse materials data into a single source of truth.
Addressing the challenges of finding sustainable material alternatives which are crucial for the engineering industry.
Leveraging machine learning for material property prediction in engineering.
Total Materia Horizon is the ultimate materials information solution, providing unparalleled access to over 570,000 metallic and non-metallic materials and provides curated, updated reference data providing:
Total Materia Integrator is a turnkey enterprise solution designed for seamless materials information management, integrating both global and your company’s private materials information into a single, secure, authoritative source.
Total Materia Predictor leverages machine learning to offer precise material property modeling and prediction, utilizing the largest curated properties dataset for unmatched accuracy.
Total Materia Green Line is designed to empower companies with the confidence in their materials' compliance and sustainability.